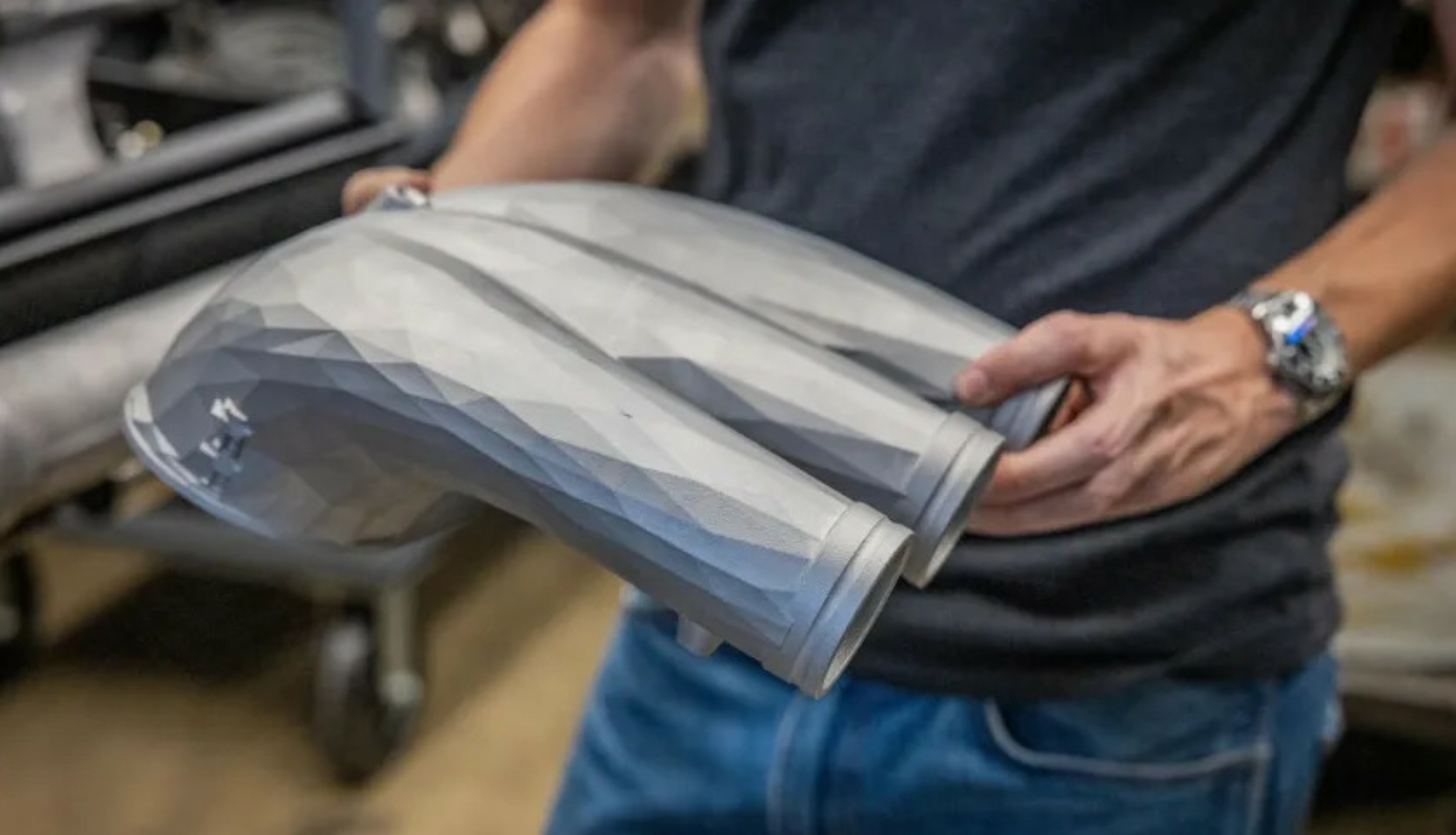
Driving Innovation: How Automotive OEMs Are Paving the Way for Electric Vehicle Manufacturing in 2025
Embracing the Shift to Electric: OEMs Lead the Charge
As the automotive industry accelerates toward an electrified future, original equipment manufacturers (OEMs) are taking the lead in shaping the next generation of electric vehicles (EVs). With governments around the world implementing stricter emissions regulations and consumers increasingly prioritizing sustainability, automakers are investing heavily in EV technology. By 2025, many OEMs plan to have electric vehicles make up a significant portion of their total vehicle offerings, with several automakers even committing to becoming fully electric within the next few decades. This ambitious shift is not just about creating new models, but about overhauling entire manufacturing processes, from supply chains to production lines, to meet the growing demand for EVs.
Advancing Battery Technology and Performance
At the heart of the EV revolution is battery technology, and OEMs are dedicating significant resources to advancing battery performance, cost-efficiency, and charging speed. Lithium-ion batteries have long been the standard, but automakers are exploring alternatives like solid-state and lithium-sulfur batteries, which promise higher energy densities and faster charging times. As battery technology improves, OEMs are also focusing on battery recycling and second-life battery usage to make the entire lifecycle of EV batteries more sustainable. By 2025, these advancements are expected to lower the overall cost of EVs, making them more accessible to the average consumer while improving the performance and range of electric models.
Collaborations and Strategic Partnerships
The path to successful EV manufacturing involves collaboration, and OEMs are forming key partnerships with tech companies, suppliers, and even competitors to accelerate innovation. These alliances are crucial for overcoming the technological challenges of EV production, particularly when it comes to autonomous driving technology, software integration, and supply chain logistics. For instance, automakers are partnering with battery manufacturers to secure a steady supply of materials and with software developers to enhance the connectivity features of electric vehicles. By 2025, strategic collaborations will play a pivotal role in helping OEMs meet production goals, improve vehicle quality, and develop new EV-related technologies.
The Road Ahead: Sustainability and Consumer Adoption
As OEMs continue to refine their EV offerings, the focus will not only be on innovation but also on sustainability and consumer adoption. Automakers are prioritizing the reduction of their carbon footprint by implementing green manufacturing practices, such as using renewable energy in production and adopting eco-friendly materials in vehicle design. Additionally, OEMs are working to educate consumers on the benefits of EV ownership, addressing concerns about range anxiety, charging infrastructure, and total cost of ownership. By 2025, as consumer confidence grows and infrastructure improves, electric vehicles are expected to become a mainstream choice, driven by both innovative OEM offerings and increased demand for sustainable transportation solutions.
The Future of Auto Parts Supply: How OEMs Are Adapting to the Changing Landscape of Sustainability and Digitalization
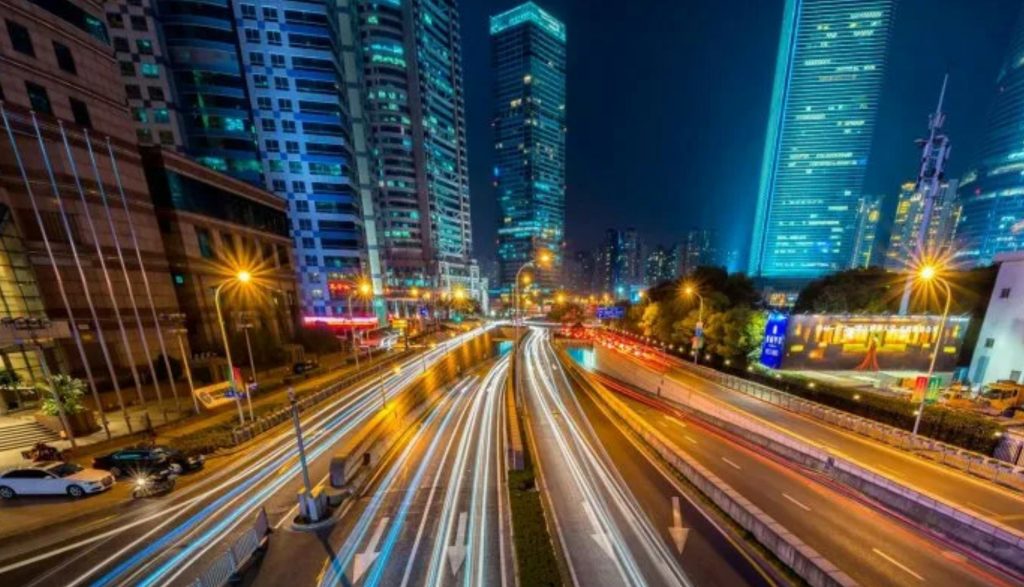
Adapting to Sustainability Demands
As the automotive industry shifts toward sustainability, original equipment manufacturers (OEMs) are rethinking their entire approach to parts supply. The rising pressure to reduce carbon footprints and improve the environmental impact of vehicles has prompted OEMs to invest heavily in sustainable practices, both in production and the sourcing of materials. With stricter global regulations on emissions and growing consumer demand for greener vehicles, OEMs are prioritizing the use of recycled and eco-friendly materials for auto parts. From bio-based plastics to sustainable metals and recyclable composites, automakers are working to ensure that the parts they produce contribute to a more sustainable future for the automotive industry. By 2025, many OEMs are expected to incorporate circular economy principles into their manufacturing processes, reducing waste and reusing materials whenever possible.
The Role of Digitalization in Auto Parts Supply
The rise of digitalization is reshaping the way OEMs manage their parts supply chains. Leveraging advanced technologies like Internet of Things (IoT), Big Data, and AI-driven analytics, automakers are gaining deeper insights into every stage of the supply chain—from raw material procurement to final assembly. This data-driven approach allows OEMs to optimize inventory management, predict demand, and minimize production delays. Through real-time data monitoring and predictive analytics, OEMs can reduce waste, improve efficiency, and ensure that parts are delivered just-in-time, reducing the need for excess stock and lowering costs. Digitalization also enables greater transparency in supply chains, allowing OEMs to trace the environmental and ethical impact of the parts they source, a critical factor in meeting sustainability goals.
Building Resilient and Flexible Supply Chains
The challenges faced during the COVID-19 pandemic highlighted the vulnerabilities in traditional auto parts supply chains, prompting OEMs to rethink how they approach supply chain resilience. Moving forward, OEMs are focusing on building more flexible and agile supply chains that can quickly adapt to disruptions. This includes diversifying suppliers, sourcing critical materials from more sustainable and geographically diverse locations, and implementing digital tools to forecast and mitigate risks. Additionally, many OEMs are investing in localization strategies, where parts manufacturing is brought closer to assembly plants to reduce dependence on overseas suppliers and long shipping routes. By incorporating more localized, diversified, and adaptable strategies, OEMs aim to create supply chains that are not only resilient but also more sustainable in the long term.
Embracing Circular Economy Principles
OEMs are increasingly incorporating circular economy principles into their auto parts supply strategies, focusing on extending the lifecycle of components and materials. By designing parts that are easier to recycle or repurpose, automakers can significantly reduce the environmental impact of their products. For instance, parts like engine components, batteries, and tires are being designed with sustainability in mind, allowing for easier disassembly and reuse at the end of their lifecycle. OEMs are also implementing take-back programs, where old parts are returned and reused in new vehicles or other applications. This approach not only supports sustainability goals but also opens up new business models for OEMs, such as remanufacturing or refurbishing auto parts for resale, helping to reduce the reliance on raw materials.
Leveraging Collaboration for Sustainability and Innovation
To successfully navigate the changing landscape of sustainability and digitalization, collaboration between OEMs, suppliers, and technology partners is critical. Automakers are working closely with material suppliers to develop and source more sustainable materials, with a focus on innovation and reducing environmental impact. Additionally, partnerships with tech companies are enabling the implementation of advanced digital tools that optimize supply chain management, track carbon emissions, and improve material traceability. Collaborative efforts also extend to the development of industry standards for sustainability, ensuring that the entire automotive ecosystem moves toward a more responsible and future-ready model. As these partnerships evolve, OEMs will continue to lead the charge in creating more sustainable and digitally optimized auto parts supply chains, setting the stage for a greener and more efficient automotive industry in the years to come.
Revolutionizing Production: How 3D Printing and AI Are Transforming the OEM Manufacturing Process
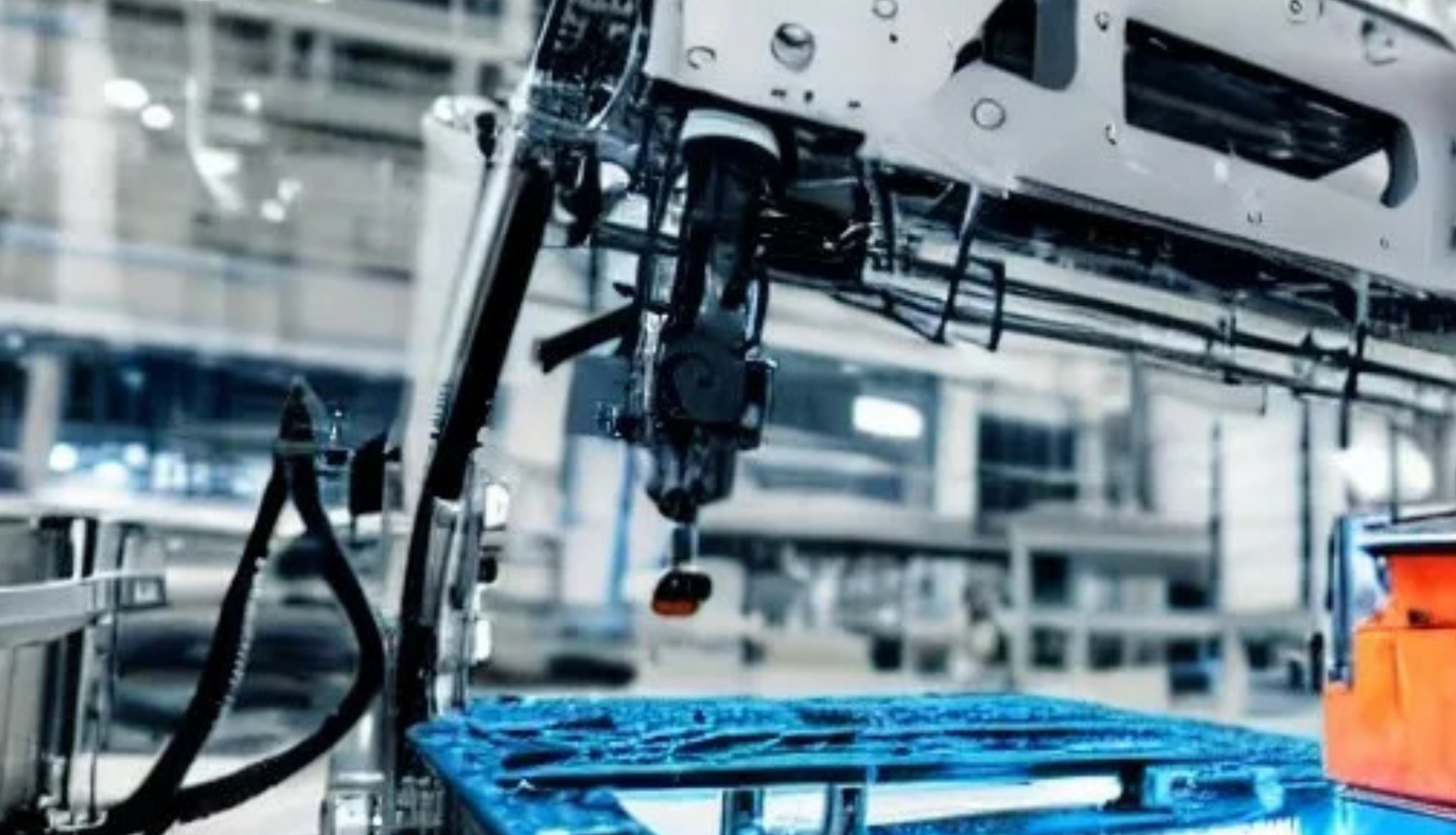
The Rise of 3D Printing in OEM Manufacturing
The automotive industry is experiencing a manufacturing revolution, driven by the convergence of 3D printing and artificial intelligence (AI). For original equipment manufacturers (OEMs), 3D printing—also known as additive manufacturing—offers a transformative way to produce complex parts more efficiently, with less waste and shorter lead times. Unlike traditional subtractive manufacturing methods, 3D printing builds parts layer by layer, which allows for the creation of intricate designs that would be difficult or impossible to achieve with conventional methods. This has significant implications for OEMs, enabling them to produce lightweight components, optimize part designs, and even create customized or on-demand parts for specific vehicle models. By 2025, many OEMs are expected to integrate 3D printing into their core production processes, unlocking new efficiencies in both manufacturing and design.
Speed and Cost Efficiency with On-Demand Production
One of the most compelling advantages of 3D printing for OEMs is its ability to accelerate the production cycle and reduce costs. Traditionally, manufacturers would have to wait weeks or even months for tooling and molds to be created for new parts, but 3D printing allows for rapid prototyping and on-demand production. This speed not only shortens time-to-market for new vehicle models or replacement parts but also enables more flexible and cost-effective production runs. In addition, OEMs can reduce inventory costs by printing parts as needed, minimizing waste and excess stock. With the ability to iterate quickly and make adjustments to designs in real-time, OEMs are finding that 3D printing allows them to be far more agile in responding to consumer demand and changing market conditions.
AI and Data-Driven Optimization of Manufacturing
Artificial intelligence (AI) is playing a key role in enhancing the capabilities of 3D printing within the OEM manufacturing process. AI-driven systems are being used to optimize part designs before they ever reach the printer, ensuring that the most efficient and effective designs are produced. By analyzing large datasets from previous manufacturing runs, AI can recommend adjustments to improve part strength, reduce material use, and enhance overall production efficiency. AI can also monitor the 3D printing process in real-time, making adjustments to ensure quality control and reduce the risk of defects. This combination of AI and 3D printing not only improves the precision and consistency of parts but also reduces errors and scrap, making the entire process more sustainable and cost-efficient.
Enhancing Customization and Flexibility
Another transformative benefit of 3D printing and AI in OEM manufacturing is their ability to enable customization on a large scale. OEMs can now produce bespoke components tailored to specific customer requirements or vehicle configurations without the need for expensive retooling or specialized production lines. This has far-reaching implications for both mass-market vehicles and specialty automotive products. For example, 3D printing can be used to create customized interior components, bespoke body parts, or even personalized performance parts that meet the exact specifications of individual customers. AI algorithms further enhance this process by streamlining the design and manufacturing workflows, ensuring that customized parts meet stringent quality standards and fit seamlessly within the vehicle’s overall design.
Sustainable Manufacturing for a Greener Future
As OEMs face growing pressure to adopt more sustainable manufacturing practices, 3D printing and AI are helping reduce the environmental impact of vehicle production. 3D printing generates less waste compared to traditional subtractive methods, as material is only used where necessary, rather than being cut away. Additionally, 3D printing allows for the use of recycled materials in manufacturing, further lowering the environmental footprint. AI-driven optimization also ensures that only the minimum required amount of material is used in each part, further reducing waste. By enabling manufacturers to produce components on-demand, these technologies also eliminate the need for large inventories, reducing the energy consumption associated with storing and transporting parts. As OEMs continue to embrace 3D printing and AI, the automotive industry is poised to make significant strides toward a more sustainable and efficient manufacturing future.