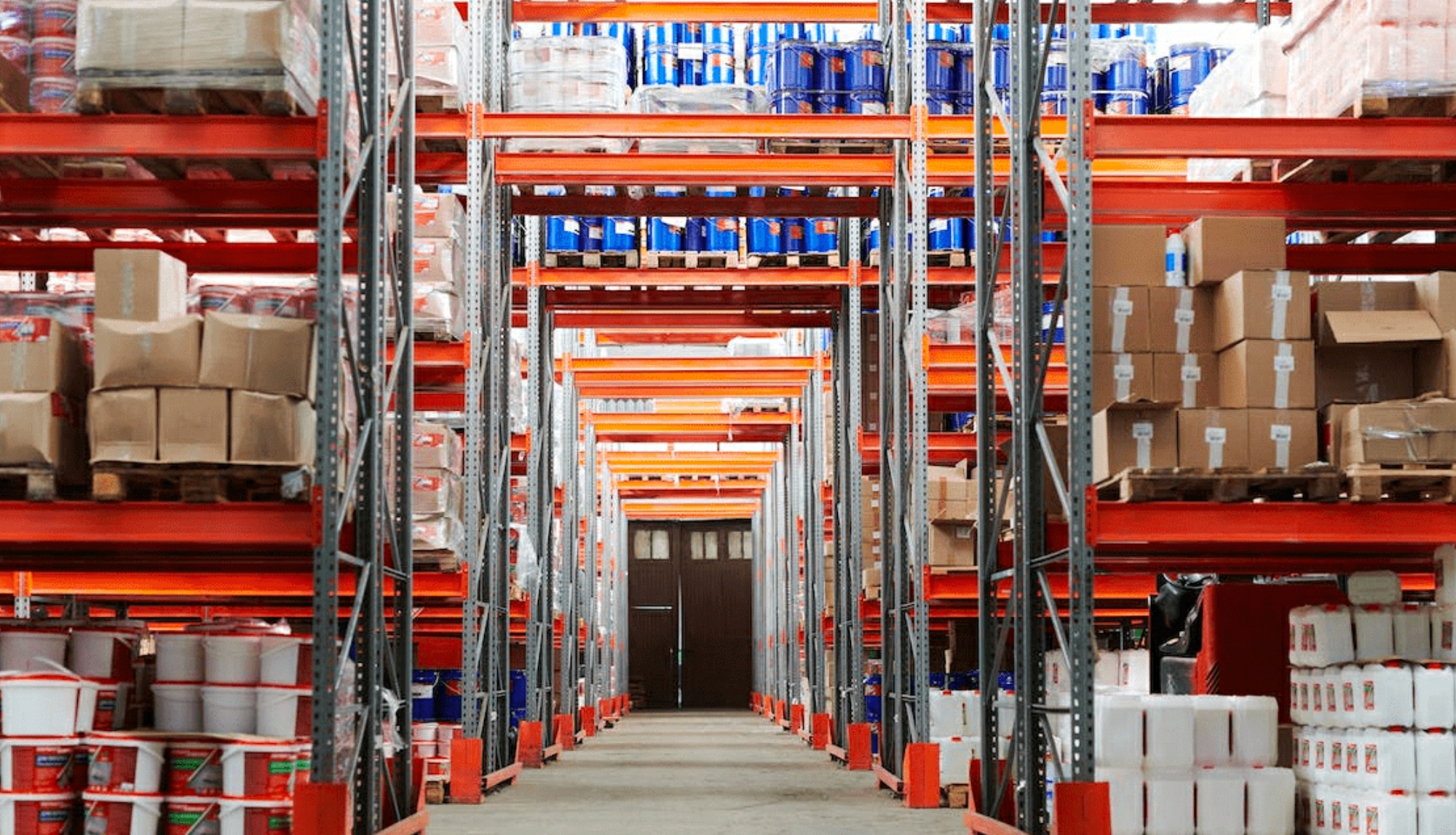
Maximizing Efficiency: 5 Key Strategies for Automotive Warehouse Distributors to Boost Inventory Management
In the fast-paced world of automotive parts distribution, warehouse efficiency is the cornerstone of a successful operation. With the increasing demand for quick turnarounds, the complexity of managing diverse product lines, and the pressure of maintaining accurate stock levels, automotive warehouse distributors must continually seek ways to streamline their inventory management. Optimizing your warehouse processes not only reduces costs but also improves customer satisfaction, making it a key competitive advantage.
Here are 5 key strategies to help automotive warehouse distributors maximize efficiency and take their inventory management to the next level:
Leverage Advanced Warehouse Management Systems (WMS)
A robust Warehouse Management System (WMS) is the backbone of any modern inventory operation. With features like real-time stock tracking, order management, and optimized picking routes, a WMS can significantly enhance the accuracy and speed of warehouse operations.
Why It Works:
- Real-Time Visibility: WMS software provides up-to-the-minute data on inventory levels, locations, and movement, allowing you to make smarter purchasing and replenishment decisions.
- Automation: WMS can automate many manual tasks such as stock counting, order allocation, and inventory reordering, reducing human error and improving order accuracy.
- Enhanced Reporting: WMS enables comprehensive reporting and analytics, offering insights into inventory turnover rates, shelf life, and product demand, all of which help in making informed business decisions.
Actionable Tip:
Invest in a scalable WMS that integrates with other systems such as your Enterprise Resource Planning (ERP) software and customer relationship management (CRM) tools. This will create a seamless flow of information across your operation.
Implement Barcode Scanning or RFID Technology
Manual inventory tracking is a major bottleneck in many warehouses. By incorporating barcode scanning or radio-frequency identification (RFID) technology, distributors can reduce the time spent on inventory counts and improve the accuracy of stock levels.
Why It Works:
- Faster Stock Movement: Barcode scanning and RFID tags speed up the stock-in and stock-out process by automating data capture and reducing manual entry errors.
- Improved Accuracy: These technologies help ensure that the correct products are picked, packed, and shipped, leading to fewer returns due to order discrepancies.
- Inventory Visibility: RFID technology, in particular, provides real-time tracking of parts, reducing stock discrepancies and making it easier to locate items quickly.
Actionable Tip:
Ensure that all parts in your warehouse are properly tagged and that your employees are trained to use the barcode scanners or RFID systems effectively.
Adopt Lean Inventory Management Practices
One of the most effective ways to improve warehouse efficiency is by adopting lean inventory management techniques. The goal of lean management is to minimize waste and maximize value by carefully controlling stock levels, improving workflows, and reducing redundancies.
Why It Works:
- Reduced Overstocking: By implementing Just-in-Time (JIT) practices and optimizing order quantities, you can avoid overstocking and the associated costs, such as storage and obsolete parts.
- Efficient Space Utilization: Lean practices encourage the consolidation of similar parts, leading to better use of warehouse space and easier access to inventory.
- Faster Turnaround: When inventory is optimized, warehouse workers spend less time searching for parts, leading to quicker order fulfillment and faster delivery times to customers.
Actionable Tip:
Regularly audit inventory to identify slow-moving parts and dead stock. Use this data to adjust stock levels and improve order accuracy.
Optimize Layout and Storage Systems for Faster Picking
A well-designed warehouse layout is critical for improving picking efficiency. By strategically organizing parts based on demand and frequency of use, you can reduce the time workers spend searching for items and improve order fulfillment speed.
Why It Works:
- Reduced Travel Time: Organizing fast-moving parts in easily accessible locations (such as the “golden zone” at eye level) allows pickers to grab items quickly, reducing the distance traveled.
- Better Product Organization: Grouping parts by category, brand, or application ensures that similar items are stored together, minimizing the risk of stockouts and errors.
- Flexible Storage Solutions: By using adjustable shelving, racks, and pallet systems, you can make better use of vertical space and adapt to varying product sizes and volumes.
Actionable Tip:
Regularly evaluate the layout to ensure that it aligns with current demand trends. For example, during peak seasons, adjust your layout to prioritize high-demand parts for faster picking.
Invest in Staff Training and Performance Monitoring
Even the best technology and processes can fall short without properly trained staff. A well-trained team is essential for maintaining operational efficiency, reducing errors, and enhancing the overall productivity of your warehouse.
Why It Works:
- Better Handling: Employees trained in proper inventory handling techniques—such as correct stacking, labeling, and sorting—will be more efficient and reduce product damage.
- Faster Pick and Pack: With proper training, warehouse workers can pick and pack orders faster, leading to quicker shipments and higher throughput.
- Data-Driven Insights: Performance monitoring tools can track employee productivity, identify bottlenecks, and highlight areas where additional training or process improvements are needed.
Actionable Tip:
Implement ongoing training programs that keep staff up-to-date on the latest technologies, warehouse safety protocols, and best practices for inventory management.
Maximizing efficiency in automotive warehouse distribution is no small feat, but by implementing these five strategies—leveraging advanced technology, optimizing your layout, adopting lean practices, and investing in staff—distributors can significantly enhance their inventory management processes. These changes not only streamline operations but also contribute to better customer service, lower operational costs, and a more competitive edge in the marketplace.
As the industry continues to evolve, staying ahead of the curve with continuous improvements and technology adoption will be key to maintaining a successful and efficient operation.
The Future of Automotive Parts Distribution: How AI and Automation Are Reshaping Warehouse Operations
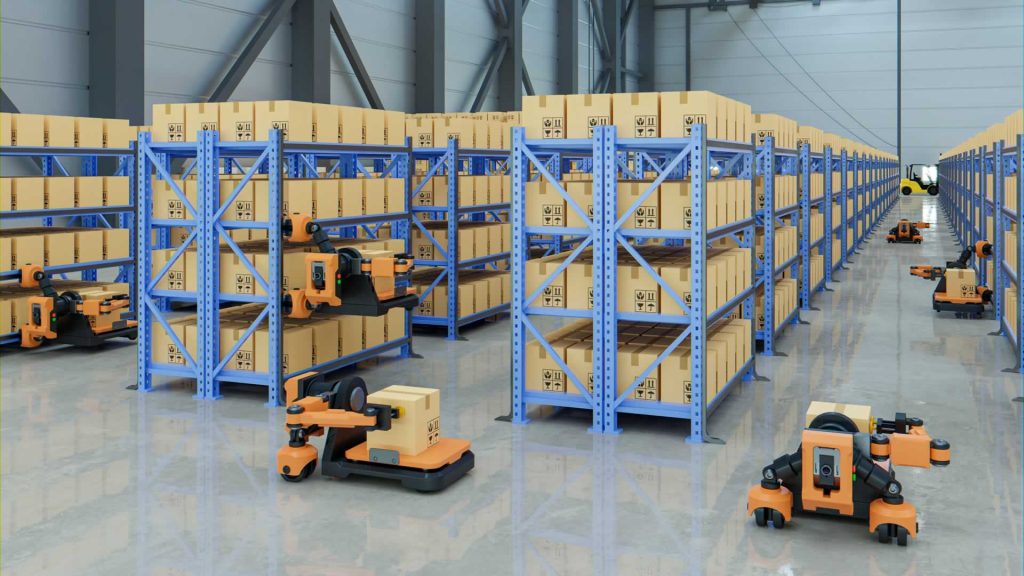
The automotive parts distribution industry is on the verge of a technological revolution. As consumer demands for faster deliveries and higher order accuracy continue to rise, warehouse operations must evolve to meet these challenges. Enter artificial intelligence (AI) and automation, two powerful forces that are already reshaping how warehouses operate and driving efficiency, cost savings, and improved customer satisfaction.
In this article, we explore how AI and automation are transforming the future of automotive parts distribution, and how these technologies are set to revolutionize warehouse operations.
AI-Powered Demand Forecasting for Smarter Inventory Management
One of the greatest challenges in automotive parts distribution is managing the ever-changing demand for parts. Traditional forecasting methods often rely on historical data, which can be inaccurate or outdated, especially in industries like automotive, where demand can be driven by seasonal trends, market shifts, and even global events. AI, however, has the capability to take forecasting to the next level.
How AI is Changing the Game:
- Predictive Analytics: AI algorithms analyze vast amounts of historical data, market trends, customer behavior, and even external factors (like economic indicators or weather conditions) to generate highly accurate demand forecasts. This enables distributors to anticipate spikes in demand and adjust inventory levels accordingly.
- Dynamic Replenishment: By integrating AI-powered demand forecasting with real-time inventory data, automotive warehouses can automatically trigger replenishment orders when stock levels drop below a certain threshold, reducing the risk of stockouts and ensuring that popular parts are always available.
Benefits:
- Reduced Overstocking: With more accurate forecasts, distributors can minimize overstocking, reducing costs associated with excess inventory and warehousing.
- Fewer Stockouts: Improved inventory planning ensures that high-demand parts are readily available, leading to faster order fulfillment and fewer delays.
Actionable Tip:
Adopt an AI-powered demand forecasting tool that integrates with your existing Warehouse Management System (WMS) to automate inventory replenishment based on predictive analytics.
Automated Picking and Packing Systems: Speeding Up Fulfillment
Warehouse picking and packing are labor-intensive processes that can often lead to bottlenecks, errors, and delays, especially in large automotive parts warehouses with complex inventory. However, automation technologies like robotic systems and conveyor belts are dramatically increasing the speed and accuracy of these tasks.
How Automation is Making a Difference:
- Robotic Picking: Autonomous robots, equipped with advanced AI, can navigate through warehouses, identify the correct parts, and pick them with remarkable accuracy. These robots can handle a variety of tasks, from retrieving small components to moving larger parts, all while optimizing the path they take to reduce travel time.
- Automated Sorting and Packing: Once picked, parts are placed onto automated sorting systems that organize them based on shipping requirements (such as size, weight, and destination). In the packing stage, automated systems use AI-driven tools to securely pack parts in boxes, optimizing space and ensuring safe transport.
Benefits:
- Increased Speed: Automation speeds up both picking and packing processes, leading to faster order fulfillment and quicker shipping times, which is crucial in meeting the growing demand for fast deliveries.
- Enhanced Accuracy: Robots and AI systems are less prone to human error, leading to fewer mistakes in picking and packing, reducing the need for returns due to incorrect orders.
Actionable Tip:
Consider integrating robotic picking and automated sorting systems into your warehouse to streamline the order fulfillment process. Start small with pilot programs and scale as you see results.
AI-Driven Predictive Maintenance for Equipment Reliability
In an automotive parts warehouse, operational downtime can be costly. Malfunctioning equipment, such as conveyor belts, forklifts, or automated picking systems, can lead to significant delays. AI-driven predictive maintenance is helping to solve this problem by proactively identifying potential issues before they cause equipment failures.
How AI is Enhancing Maintenance:
- Real-Time Monitoring: AI systems can monitor the performance of warehouse equipment in real time, using sensors and IoT (Internet of Things) devices to track variables like temperature, vibration, and power usage. By analyzing this data, AI can detect anomalies that might signal an impending failure.
- Predictive Analytics: Instead of relying on scheduled maintenance, AI systems predict when a machine is likely to fail and recommend maintenance actions based on usage patterns and wear-and-tear data. This approach helps minimize unplanned downtime.
Benefits:
- Reduced Downtime: By predicting when equipment will need maintenance, distributors can address issues before they lead to costly breakdowns, ensuring smooth and continuous operations.
- Lower Maintenance Costs: Predictive maintenance allows for more efficient use of resources by addressing issues at the right time and preventing unnecessary repairs or parts replacement.
Actionable Tip:
Implement AI-powered predictive maintenance tools that integrate with your equipment management system to optimize the lifespan of your warehouse machinery and reduce maintenance costs.
AI-Powered Supply Chain Optimization
The automotive parts distribution network is often complex, involving multiple suppliers, manufacturers, and transport providers. AI is now playing a pivotal role in optimizing supply chain logistics, ensuring that the right parts arrive at the right time, at the lowest possible cost.
How AI is Optimizing Supply Chains:
- Route Optimization: AI algorithms can analyze traffic patterns, weather, and other variables in real time to determine the most efficient delivery routes for transport vehicles, reducing fuel costs and delivery times.
- Supply Chain Visibility: AI tools provide end-to-end visibility into the supply chain, allowing warehouse managers to track shipments, monitor stock levels, and make adjustments in real time to avoid delays or disruptions.
- Automated Ordering: AI can automate the process of ordering parts from suppliers based on real-time stock levels and demand forecasting, reducing manual intervention and ensuring a seamless flow of inventory.
Benefits:
- Faster Deliveries: Optimized logistics lead to faster shipping times, improving customer satisfaction and ensuring that parts are available when needed.
- Cost Savings: By optimizing routes and supply chain processes, AI can help reduce transportation and operational costs.
Actionable Tip:
Integrate AI-based supply chain management tools with your WMS to improve coordination between suppliers, transportation providers, and your warehouse, ensuring timely and cost-efficient deliveries.
AI and Automation in Customer Service
AI is not only transforming warehouse operations but also revolutionizing customer service. AI chatbots and virtual assistants can handle customer inquiries, track order statuses, and provide real-time updates without the need for human intervention. This is especially useful in the automotive parts distribution industry, where customers often need quick, accurate answers to urgent questions.
How AI is Enhancing Customer Service:
- Chatbots and Virtual Assistants: AI-powered chatbots can provide instant responses to customer queries, such as checking part availability, tracking orders, or even processing returns. These bots can learn from previous interactions and improve over time, offering increasingly accurate and relevant information.
- Automated Order Updates: AI systems can automatically send notifications about order statuses, estimated delivery times, or changes in stock availability, keeping customers informed throughout the buying process.
Benefits:
- Improved Customer Experience: AI-powered systems can provide faster, more accurate responses to customer inquiries, leading to higher satisfaction and loyalty.
- Cost Efficiency: Automation of customer service tasks reduces the need for large customer service teams, freeing up resources for other areas of the business.
Actionable Tip:
Incorporate AI chatbots into your website or customer portal to handle common customer inquiries and provide real-time order updates, reducing wait times and improving satisfaction.
AI and automation are reshaping the future of automotive parts distribution, enabling warehouses to operate faster, smarter, and more cost-effectively. From AI-driven demand forecasting and predictive maintenance to automated picking and AI-powered customer service, these technologies are providing distributors with the tools they need to stay competitive in an increasingly demanding market.
By adopting these innovations, automotive parts distributors can streamline operations, enhance customer satisfaction, and reduce costs, ensuring that they are well-equipped to meet the demands of tomorrow’s automotive supply chain. The future is automated—and those who embrace these changes today will be the leaders of tomorrow.
Navigating Supply Chain Challenges: Essential Best Practices for Automotive Warehouse Distributors for 2025
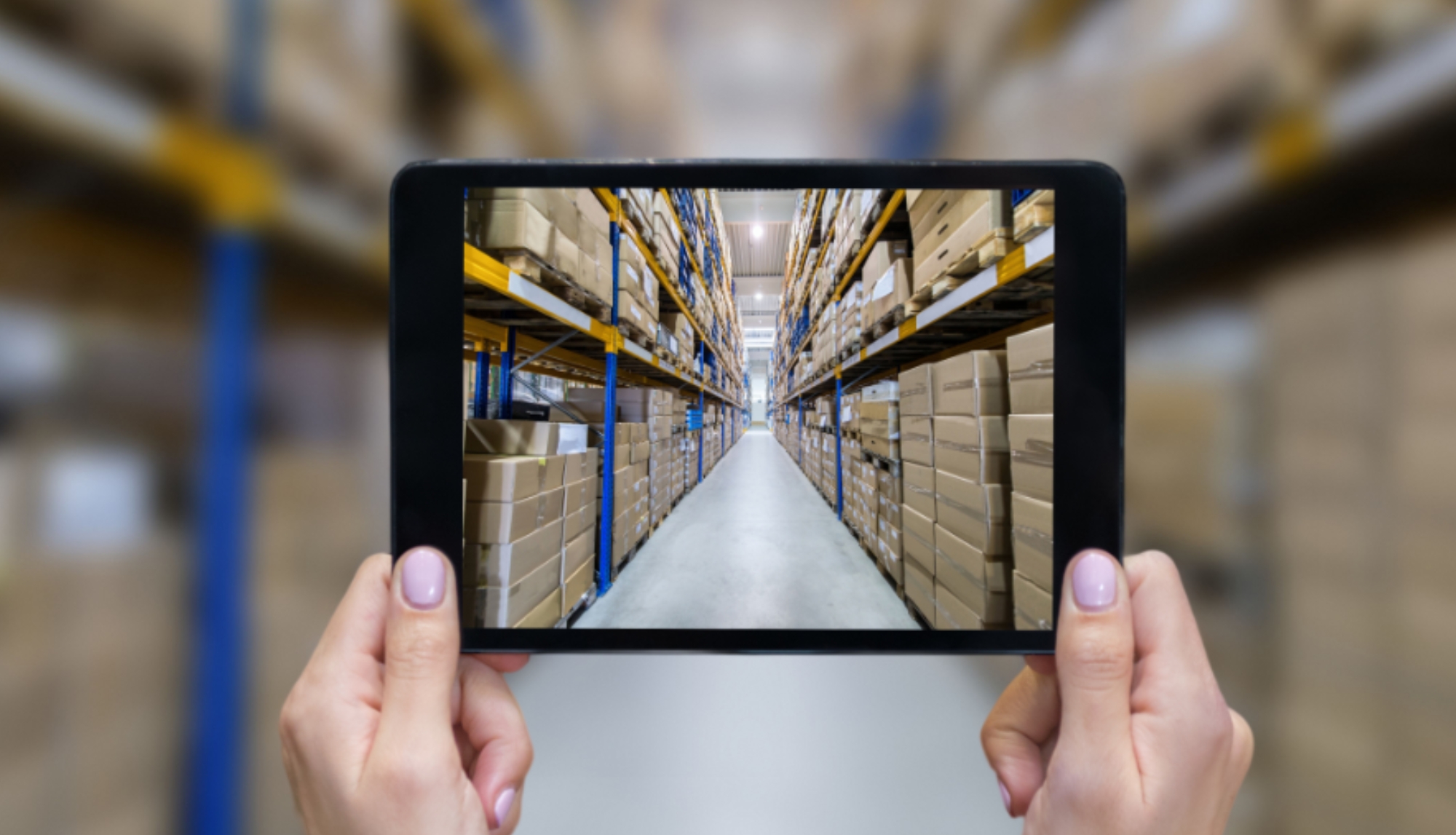
Supply chain management in the automotive industry is a complex and challenging task. With the rapid advancements in technology, changing consumer demands, and increasing global competition, automotive warehouse distributors are facing a variety of challenges. To stay ahead in the game and ensure smooth operations, it is crucial for warehouse distributors to implement best practices that are tailored to the unique needs of the industry. In this article, we will explore some essential best practices that automotive warehouse distributors should adopt to navigate supply chain challenges in 2025.
Implementing Advanced Technology Solutions
One of the key challenges faced by automotive warehouse distributors is the need to efficiently manage inventory, streamline operations, and meet customer expectations in a fast-paced environment. To address these challenges, warehouse distributors should invest in advanced technology solutions such as automated inventory management systems, RFID tracking, and warehouse management software. These tools can help improve efficiency, reduce errors, and enhance visibility across the supply chain.
Embracing Data Analytics and Predictive Maintenance
Data analytics plays a crucial role in optimizing supply chain operations and improving decision-making processes. By leveraging data analytics tools, warehouse distributors can gain valuable insights into inventory levels, demand forecasting, and supplier performance. Additionally, predictive maintenance technologies can help prevent equipment breakdowns and minimize downtime, thus ensuring continuous operations and customer satisfaction.
Strengthening Supplier Relationships
In the automotive industry, a strong and reliable network of suppliers is essential for a smooth supply chain operation. Warehouse distributors should prioritize building strong relationships with key suppliers, fostering open communication, and collaborating on process improvements. By working closely with suppliers, warehouse distributors can ensure timely delivery of parts and components, reduce lead times, and enhance overall supply chain efficiency.
Investing in Talent Development and Training
The success of a warehouse distribution operation depends heavily on the skills and expertise of its workforce. To navigate supply chain challenges in 2025, automotive warehouse distributors should invest in talent development programs and provide ongoing training to employees. By equipping staff with the necessary skills and knowledge, warehouse distributors can enhance productivity, reduce errors, and adapt to changing market dynamics effectively.
Enhancing Sustainability Practices
As consumers become increasingly environmentally conscious, automotive warehouse distributors are under pressure to adopt sustainable practices in their operations. To address this challenge, distributors should implement sustainability initiatives such as reducing carbon emissions, minimizing waste, and promoting eco-friendly packaging solutions. By incorporating sustainability practices into their supply chain operations, warehouse distributors can enhance their corporate image, attract environmentally conscious customers, and contribute to a greener future.
Ensuring Regulatory Compliance
The automotive industry is highly regulated, with strict quality and safety standards that warehouse distributors must adhere to. To navigate supply chain challenges in 2025, distributors should stay informed about regulatory changes, ensure compliance with industry standards, and conduct regular audits to identify and address any gaps in their operations. By maintaining compliance with regulations, warehouse distributors can avoid costly penalties, protect their reputation, and build trust with customers.
In conclusion, navigating supply chain challenges in the automotive industry requires a holistic approach that addresses technological advancements, data analytics, supplier relationships, talent development, sustainability practices, and regulatory compliance. By implementing these essential best practices, warehouse distributors can optimize their operations, enhance efficiency, and stay competitive in the ever-evolving automotive market of 2025.