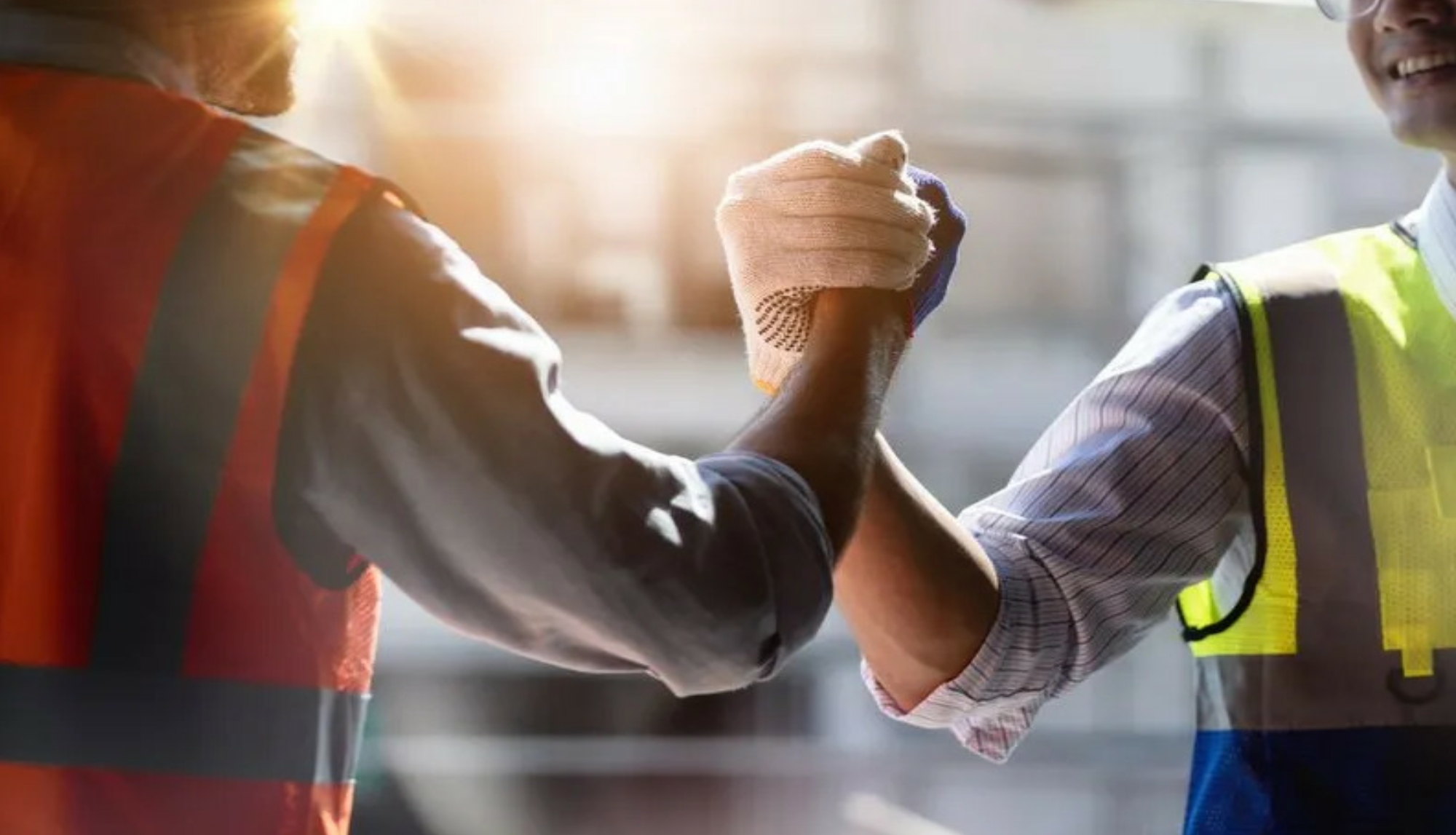
Manufacturing Excellence Through Outsourcing: How Employee Leasing Powers Productivity and Innovation
The Changing Landscape of Manufacturing
In today’s rapidly evolving industrial environment, the pressures of globalization and technological advancements have forced manufacturers to rethink their strategies. Traditional models that relied heavily on in-house teams are being challenged by innovative alternatives that promise greater efficiency and adaptability. Among these, employee leasing has emerged as a powerful solution, allowing companies to tap into a pool of skilled workers while maintaining flexibility and focus on core business operations. This trend not only drives productivity but also opens doors to innovation in an increasingly competitive marketplace.
Employee Leasing
Employee leasing is a practice where a company contracts with a third-party service provider to handle labor needs, effectively leasing staff instead of hiring them directly. This arrangement can take many forms, ranging from temporary staffing solutions to outsourcing entire departments. For manufacturers, this means gaining access to a wide array of specialized skills without the long-term commitment or overhead costs associated with permanent hires. By leveraging the expertise of an employee leasing firm, manufacturers can swiftly adapt to shifting demands while ensuring that their workforce remains agile and responsive.
Elevating Productivity Through Flexibility
One of the most significant benefits of employee leasing is the immediate boost to productivity that comes from a more flexible workforce. In a manufacturing setting, workloads can fluctuate due to seasonal demands, new product launches, or unpredictable market conditions. Employee leasing allows businesses to scale their workforce up or down according to their current needs, eliminating the inefficiencies associated with maintaining a bloated in-house team. This flexibility not only enhances operational efficiency but also empowers manufacturers to meet customer demands swiftly, fostering a more responsive production line.
Fostering Innovation by Accessing Diverse Talent
Innovation lies at the heart of manufacturing excellence, and employee leasing enables companies to access a diverse array of talent and expertise that can spark new ideas and approaches. By partnering with specialized staffing agencies, manufacturers can bring in professionals with unique insights and experiences that challenge the status quo. This influx of fresh perspectives can lead to the development of cutting-edge products, optimization of existing processes, and the implementation of new technologies, driving competitiveness and market leadership. When companies harness this potential, they not only improve their offerings but also stimulate a culture of creativity that permeates every level of the organization.
Building Stronger Relationships and Community Impact
Another advantage of employee leasing is the opportunity to build stronger relationships with staffing partners and local communities. By collaborating closely with leasing organizations, manufacturers can create a pipeline of talent tailored to their specific needs, while also supporting local workforce development initiatives. In return, they gain not just a flexible labor solution but also a dedicated team that is invested in the company’s success. This relationship can enhance morale and retention among leased employees, as they may feel more aligned with their work and contribute positively to the company culture. Furthermore, by investing in local talent, manufacturers can play a crucial role in sustaining economic growth within their communities.
The Future of Manufacturing is Collaborative
As manufacturers continue to navigate the complexities of modern industry, embracing employee leasing can be a transformative strategy that enhances both productivity and innovation. By tapping into flexible workforce solutions, companies can respond swiftly to changes in demand, harness diverse skills to foster innovation, and build stronger connections with their communities. The future of manufacturing lies not only in advanced technology and efficiency but also in collaborative approaches to workforce management that empower organizations to thrive in a dynamic landscape. In this way, outsourcing through employee leasing isn’t just about cutting costs; it’s about creating a sustainable path toward manufacturing excellence that benefits all stakeholders involved.
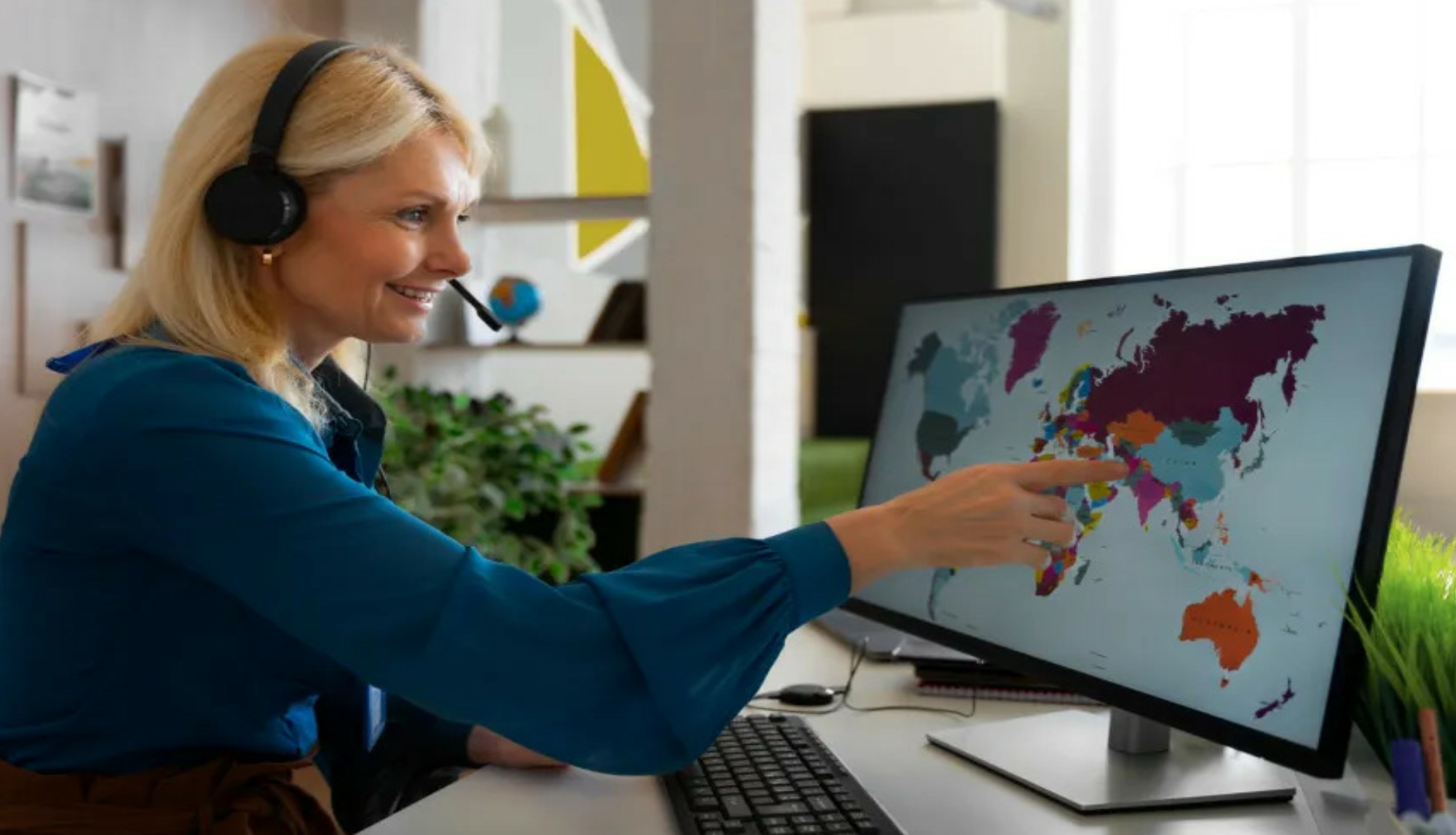
Global Talent for Manufacturers: The Benefits of Remote Staffing in Modern Production Lines
Embracing a New Era in Manufacturing
In an increasingly interconnected world, the manufacturing sector is undergoing a remarkable transformation. Traditionally, manufacturers relied heavily on local talent, crafting a workforce from the surrounding communities. However, the advent of remote staffing is changing the game, allowing companies to tap into a global pool of expertise. This shift is not merely a response to challenges posed by events like the COVID-19 pandemic; it is also an opportunity for manufacturers to innovate and enhance their production lines. Embracing this new era could be the key to staying competitive and adapting to evolving market demands.
Access to a Diverse Skill Set
The evolution of remote staffing opens the door to a diverse array of talent that manufacturers may not find locally. Global recruitment allows companies to select experts for specific roles, such as data analysts, engineers, and software developers, regardless of their geographical location. Picture a software engineer in Eastern Europe collaborating seamlessly with a design team in North America to optimize the production line. This sort of collaboration enriches the workplace culture and enhances innovation, as diverse perspectives lead to creative solutions that may not have emerged in a more homogeneous team. Ultimately, attracting top-tier talent from around the world can facilitate a more efficient and creative production process.
Cost-Effectiveness and Flexibility
A significant benefit of remote staffing is the cost savings it can provide. Manufacturers can reduce expenses associated with physical office spaces, utilities, and local salaries, which may be exorbitant in certain regions. By employing remote workers in areas with lower costs of living, businesses can retain highly skilled personnel while significantly decreasing operational overhead. Beyond the immediate financial benefits, remote staffing also grants greater flexibility. As production needs fluctuate—whether due to seasonal demand or project-specific tasks—companies can scale their workforce up or down without the long-term commitments that traditional hiring entails.
Enhanced Productivity and Focused Expertise
When given the chance to work remotely, many employees report higher levels of job satisfaction and productivity. Remote work eliminates commutes and often provides a more comfortable working environment, which can significantly enhance focus. For manufacturers, this means that specialists can dedicate their time to tasks that require deep concentration and expertise, such as process engineering or quality assurance, resulting in improved output quality. Furthermore, remote teams can operate across multiple time zones, allowing for extended hours of productivity and quicker turnarounds on projects, ensuring production lines run efficiently.
Promoting Sustainability in Manufacturing
As companies worldwide move towards a more sustainable future, remote staffing can play a crucial role in this transition. By reducing the need for physical office spaces and commuting, manufacturers can decrease their carbon footprints. Employing remote talent also allows manufacturers to be more agile, quickly adapting their processes to incorporate sustainable practices without the overhead of traditional systems. Moreover, as businesses embrace sustainable production lines, they can leverage the expertise of remote talent specialized in green technology and processes, ensuring that their operations align with global sustainability goals.
The Future of Manufacturing is Remote
The incorporation of remote staffing in manufacturing represents a groundbreaking shift that offers numerous advantages. By engaging a global talent pool, manufacturers can access specialized skills, enhance productivity, and reduce costs—all while promoting a more sustainable industry. As the manufacturing landscape continues to evolve, companies that embrace this remote work approach will not only remain competitive but will also set a precedent for a more innovative, efficient, and environmentally-conscious future. The world is becoming smaller and more connected, and manufacturers who adapt will undoubtedly thrive in this new paradigm.