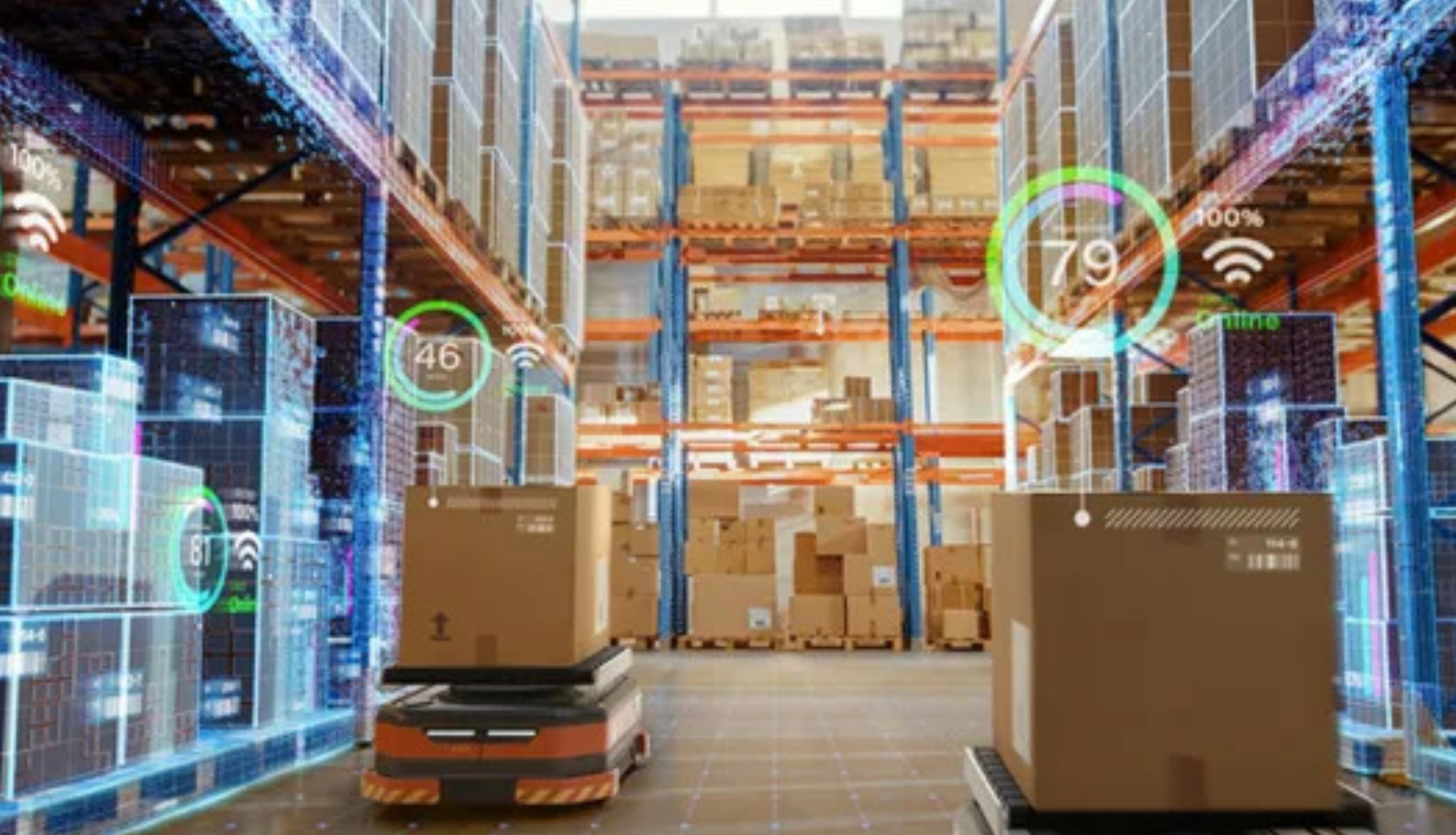
Optimizing Warehouse Operations: The Future of Automotive Parts Distribution
The Rise of Automation
One of the key trends shaping the future of automotive parts distribution is the rise of automation. From automated guided vehicles (AGVs) to robotic pickers, warehouses are increasingly turning to technology to streamline their operations. By automating routine tasks, companies can reduce labor costs, increase efficiency, and minimize human error. This not only speeds up order fulfillment but also improves inventory accuracy, leading to higher customer satisfaction.
Data-Driven Decision Making
Another crucial aspect of optimizing warehouse operations is the use of data-driven decision-making. With the help of advanced analytics tools, companies can track key performance metrics, such as order processing time, inventory turnover, and picking accuracy. By analyzing this data, warehouse managers can identify bottlenecks, optimize workflows, and make informed decisions to improve overall efficiency. This focus on data allows companies to stay agile and responsive to changing market demands.
Embracing Sustainable Practices
As concerns about environmental sustainability continue to grow, automotive parts distributors are also focusing on reducing their carbon footprint. By optimizing warehouse layouts, implementing energy-efficient lighting, and minimizing waste, companies can not only lower their operating costs but also contribute to a greener future. Sustainable practices not only benefit the environment but also enhance brand reputation and attract eco-conscious customers.
Adopting Just-In-Time Inventory Management
Just-in-time (JIT) inventory management is another strategy that is gaining popularity in the automotive parts distribution sector. By stocking only the parts needed for immediate orders, companies can reduce inventory holding costs and free up valuable warehouse space. This lean approach to inventory management helps companies minimize waste, improve cash flow, and respond quickly to changing customer demands. By optimizing their inventory levels, companies can achieve higher fill rates and reduce backorders.
Investing in Employee Training and Development
While technology plays a key role in optimizing warehouse operations, it is essential not to overlook the human element. Investing in employee training and development is crucial to ensure that staff are equipped with the skills and knowledge needed to succeed in a rapidly evolving industry. By offering continuous training programs, companies can empower their workforce, boost morale, and foster a culture of innovation. Engaged and well-trained employees are more likely to take ownership of their work, leading to higher productivity and customer satisfaction.
Enhancing Customer Experience
Ultimately, the goal of optimizing warehouse operations is to enhance the overall customer experience. By leveraging technology, data, sustainability practices, lean inventory management, and employee development, companies can deliver faster, more accurate, and cost-effective service to their customers. This focus on continuous improvement not only drives operational efficiency but also strengthens customer loyalty and drives long-term success in the competitive automotive parts distribution industry.
Optimizing warehouse operations is essential for companies in the automotive parts distribution sector to stay competitive and meet the evolving needs of customers. By embracing automation, data-driven decision-making, sustainability practices, JIT inventory management, employee training, and focusing on enhancing the customer experience, companies can position themselves for success in the future. By humanizing these strategies and prioritizing the well-being of both employees and customers, companies can build a strong foundation for growth and innovation in the dynamic automotive industry.
The Role of Automation in Modern Automotive Parts Warehouses
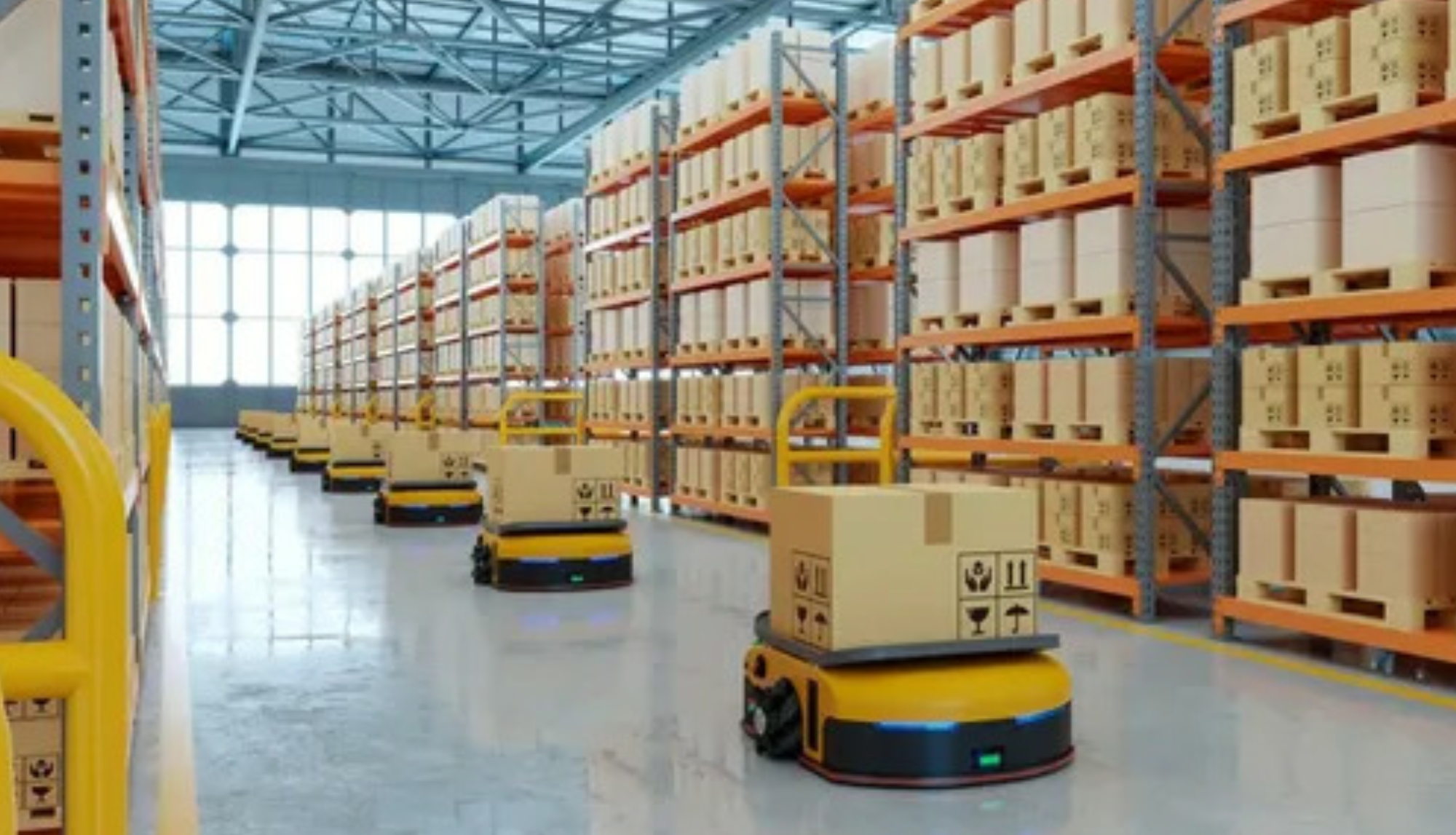
Increased Efficiency and Accuracy
One of the key benefits of automation in automotive parts warehouses is the increased efficiency and accuracy it provides. Automated systems can quickly and accurately locate parts in the warehouse, reducing the time it takes for workers to find and retrieve them. This not only speeds up the process of fulfilling orders but also reduces the likelihood of errors, ensuring that the right parts are delivered to the right customers every time.
Improved Inventory Management
Automation also plays a crucial role in improving inventory management in automotive parts warehouses. Automated systems can track inventory levels in real-time, making it easier for warehouse managers to monitor stock levels and reorder parts as needed. This helps to prevent stockouts and excess inventory, leading to cost savings and improved customer satisfaction.
Enhanced Safety for Workers
Automation in automotive parts warehouses also contributes to enhanced safety for workers. By automating repetitive and potentially hazardous tasks, such as lifting heavy parts or operating machinery, automation reduces the risk of injuries in the warehouse. This not only creates a safer working environment for employees but also helps to reduce the number of workplace accidents and associated costs.
Streamlined Order Fulfillment
Another benefit of automation in modern automotive parts warehouses is streamlined order fulfillment. Automated systems can quickly process orders, pick the necessary parts from storage, and package them for shipping. This not only speeds up the order fulfillment process but also allows warehouses to handle a larger volume of orders with greater efficiency.
Customer Satisfaction
Automation in automotive parts warehouses ultimately leads to improved customer satisfaction. By enhancing efficiency, accuracy, and speed in fulfilling orders, automation ensures that customers receive their parts promptly and in perfect condition. This helps to build trust with customers and create a positive reputation for the warehouse, ultimately leading to repeat business and referrals.
Empowering Workers with Technology
While automation plays a critical role in modern automotive parts warehouses, it is important to recognize that it is not meant to replace human workers but rather to empower them with technology. By automating repetitive tasks and allowing workers to focus on more complex and value-added activities, automation humanizes the industry by helping workers to develop new skills and take on more rewarding roles within the warehouse.
Automation in modern automotive parts warehouses is revolutionizing the industry by increasing efficiency, improving accuracy, enhancing safety, streamlining order fulfillment, and ultimately, improving customer satisfaction. By empowering workers with technology and allowing them to focus on higher-level tasks, automation is humanizing the industry and creating a more sustainable and efficient warehouse environment for years to come.
From Warehouse to Customer: How Distributors Are Improving Last-Mile Delivery
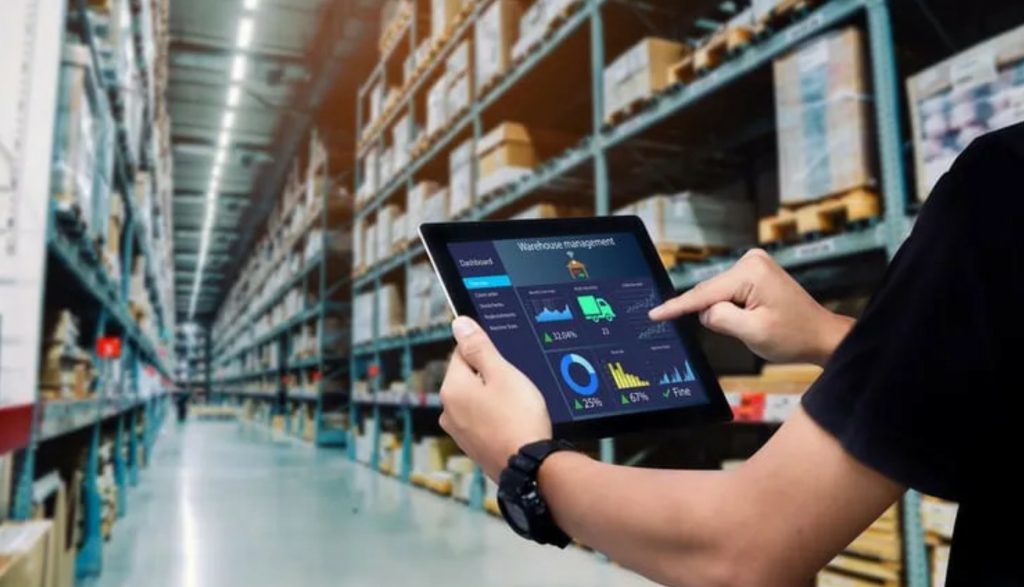
Customer-Centric Approach
Distributors understand the importance of putting the customer first. They are implementing customer-centric strategies to ensure a seamless delivery experience. From providing real-time tracking information to offering flexible delivery options, distributors are going the extra mile to meet the unique needs of each customer.
Technology Integration
Technology plays a significant role in improving last-mile delivery. Distributors are leveraging cutting-edge technology such as route optimization software and GPS tracking to streamline the delivery process. This not only improves efficiency but also allows customers to track their packages in real-time, giving them peace of mind knowing exactly when their order will arrive.
Sustainability Initiatives
In today’s environmentally conscious world, sustainability is a key focus for many distributors. From using electric vehicles for deliveries to implementing eco-friendly packaging solutions, distributors are taking steps to reduce their carbon footprint. By prioritizing sustainability, distributors are not only improving the last-mile delivery experience but also contributing to a greener future for all.
Customer Communication
Effective communication is essential in the last-mile delivery process. Distributors are proactively communicating with customers every step of the way, from order confirmation to delivery updates. By keeping customers informed and engaged, distributors are building trust and loyalty, ultimately enhancing the overall delivery experience.
Delivery Partnerships
Collaboration is key in the world of last-mile delivery. Distributors are forming strategic partnerships with local delivery services and gig economy platforms to expand their reach and improve delivery speed. By working together, distributors can meet the growing demand for fast and reliable deliveries, ensuring customers receive their orders on time every time.
Personalized Touch
In a digital world, personalization sets distributors apart from the competition. From handwritten notes to custom packaging, distributors are adding a personalized touch to each delivery. This humanizes the last-mile delivery experience, making customers feel valued and appreciated. By going the extra mile to make each delivery special, distributors are creating memorable experiences that keep customers coming back for more.
Distributors are constantly innovating and humanizing the last-mile delivery experience for customers. By putting the customer first, leveraging technology, prioritizing sustainability, improving communication, forming partnerships, and adding a personalized touch, distributors are revolutionizing the way packages are delivered from warehouses to customers. With these initiatives in place, the future of last-mile delivery looks promising, with a focus on efficiency, sustainability, and customer satisfaction.